Anderson Roofing and Exteriors is the top covering of a building, protecting it against rain, snow, sunlight, and temperature extremes. Roofs can be constructed in a wide variety of forms.
When you reroof your home, the materials you choose will significantly impact your initial construction costs and long-term energy costs.
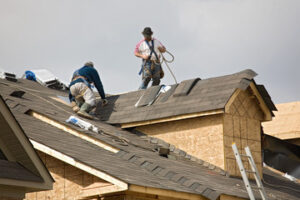
Rafters are a key part of traditional stick framing and provide a sturdy base for roof decks, shingles, or other roofing materials. They also serve as a structural framework to help distribute weight evenly across the structure, preventing it from sagging or developing other problems over time. Rafters can be reinforced with additional components like collar ties to increase their strength and stability.
A rafter is a long wooden board that creates the roof frame, or stick framing, in a home or other building. They are typically cut on-site and fastened to ceiling joists and the exterior walls of the building. Rafter boards are usually 2x10s or 2x12s and slope down from the peak of the roof. A ridge board or ridge beam helps support the rafters at their highest point and is secured with collar ties.
Unlike trusses prefabricated in a factory, rafters can be built on-site to meet specific dimensions. This provides greater design flexibility for homeowners and builders. It also allows for features like vaulted ceilings to be incorporated into the structure.
Another advantage of rafters is that they are easy to repair, particularly for older structures that have experienced some sagging or other structural issues. A professional roofer will be able to assess the condition of a rafter and recommend any repairs or replacements needed.
Roof trusses are an alternative to traditional rafter framing and can be used in various applications. These structures have a triangular design, giving them a high level of resistance to different stresses. They also allow designers to create unique interior spaces without needing load-bearing walls.
A truss comprises top and bottom chords that join in a triangle, with internal web members connecting the chords. The combination of timber and metal connector plates at the truss junctions supports the roof loadings. It also ensures the structure remains stable and meets building codes and standards.
Modern trusses are fabricated from lumber and connected with metal plate-to-plate joints rather than nails or screws. They are designed with sophisticated software that accurately calculates and distributes the structural loads throughout the truss. They can be produced quickly and easily at the factory.
To install a truss, first prepare the work area by clearing it of any debris and marking its layout. Position the first truss at one end of the structure and carefully align it with its layout marks. Temporarily secure it with braces until the rest of the trusses are in place. Once the trusses are in place, it is time to attach sheathing. The trusses should be inspected for alignment and spacing before sheathing is installed. Any trusses that are distorted or twisted should be corrected immediately.
The purlins in your metal building roof carry the weight of the roof deck and transfer loads to the primary structural elements supporting the roof. They are usually placed at regular intervals across the roof.
The load-bearing capacity of a purlin is determined by its cross-sectional properties. The most common purlin section is the C-section, although z-section purlins and other types are also available. The type of material used for the purlins is also important, as it affects their strength and durability. Steel and aluminum purlins are popular choices for metal framing because they can resist corrosion and other environmental conditions better than wood.
The purlins in a metal roof frame have several purposes, and they are crucial for maintaining the integrity of your building. They provide a platform for installing insulation materials and other services and assist in adjusting the roof pitch or slope. This is necessary to prevent water accumulation and damage to the structure.
The flanges on the edges of purlins make them ideal for distributing loads evenly across rafters or trusses. This distribution reduces the overall stress on a single truss or rafter and increases the structural stability of a roof or other structures. Purlins should always be bolted rather than welded, as welding can affect the cold-formed steel and add significant stress connections. Welding can also remove the protective coating on the steel, which can lead to premature corrosion and reduced durability.
A ridge board is a non-structural member that spans a roof’s ridge (peak). It provides a nailing surface and point of bearing for opposing roof rafters and is usually covered with ridge tiles or another covering. The ridge is also the location of rafter ties, which resist the outward thrust that rafters apply to the exterior walls of a home.
Unlike a ridge board, a ridge beam is structural and must be designed to support the loads placed on it by the rafters it supports. It is required by code where the roof slope is less than 3 in 12 units horizontal or 25-percent slope (IRC section R802.3).
One of the primary benefits of a ridge beam is that it eliminates the need to balance rafters against each other, which can lead to miscalculation errors. It also helps to resist sagging and twisting of the roof trusses and ceiling joists that occur over time.
A ridge beam is usually constructed with two 2x pieces of lumber notched at each end to accept rafter ties. These ties are then screwed to the ends of the ridge beam. However, other types of framing products, such as LVL and Microllam, are also being used by framers to create ridge beams. This method can be more cost-effective than using two separate pieces of dimension lumber for a ridge beam.
The king post is a central support structure for roof framing. It is usually made of wood and is designed to bear great weight. It is the main load-bearing element in a truss and evenly transfers the roof’s weight to the principal rafters. The king post also helps distribute the truss’s load more effectively and prevents overload.
In modern timber framing, a king post truss is often used with a collar tie truss to span a loft area or large living space. Its simple design makes it easy to construct and is relatively cost-effective. Additionally, king post trusses are easy to maintain and repair, saving builders time and money.
Another common use for king posts is in retaining walls. They are installed at a few meter centers along a construction line and then filled with concrete panels, blocks, brick, or stone to create an effective retaining wall.
Traditionally, a king post is constructed with a long tenon and mortise, which can be difficult to fit correctly. The tenon must be cut to the right length and fitted into the mortise without any gaps or looseness. This can be challenging, especially if the tenon is a piece of white oak, which is extremely hard and brittle. It is important to ensure the tenon and mortise are correctly aligned, as any deviations can compromise the strength of the truss.
Aside from their durability, another reason homeowners are increasingly choosing synthetic shingles is their environmental friendliness. These shingles are produced with recycled material; many are even completely recyclable after use. Additionally, the manufacturers of these shingles often incorporate advanced UV inhibitors that help decrease wear from the sun’s harsh rays.
Many of these shingles are backed by an industry-leading 50-year warranty, which adds further value and peace of mind to the homeowner. They are much lighter than their authentic slate and wood alternatives, making them easier to install. Plus, they don’t require additional reinforcement to the home’s framing like a traditional slate or wood roof.
While it may seem counterintuitive, synthetic shingles are more energy efficient than their natural alternatives. This is because the advanced UV inhibitors in these shingles help reflect the sun’s heat and rays. This reduces the demand for air conditioning systems and decreases the infamous “heat-island” effect experienced in heavily populated areas.
In addition, these shingles’ safety features are unparalleled compared to cedar and slate. Unlike those two popular roofing options, they are Class-A fire-rated, with the highest possible rating for roof materials. That means they are not flammable and resist the spread of fire, providing you with the utmost safety and protection for your family.
If you’re considering a new synthetic roof, we recommend you consult a professional roofer to determine your best option. Our team of experts is ready to guide you through the entire process. To start, schedule your free roofing inspection by clicking the button below!